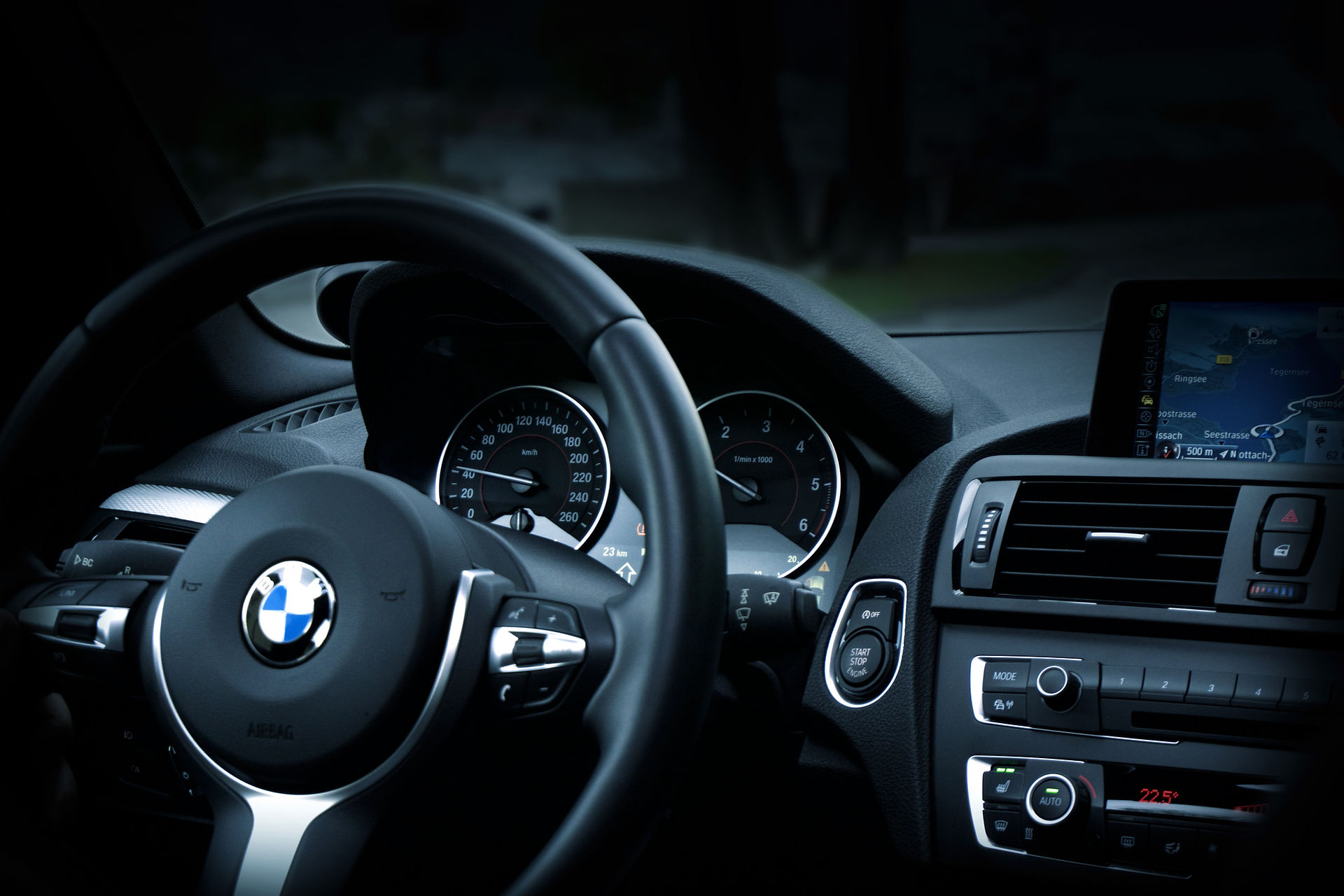
No Smoke No Poke
Diesel Tuning / DPF Removal and Smoke Emissions
​
Basic engineering fact - Smoke is WASTED energy This is the product of a badly written calibration, by normally adding fuel because its the easy and quick map to find with absolutely no recognition to thermodynamic principles,stoichiometry or Volumetric efficiency.
A correctly written calibration will provide the cylinder with the correct amount of air to completely combust the given fuel. PLEASE understand that fuel is fixed sum (energy) for the ECU and air is variable, an engine is driven by the heating of air to gain the most power you must heat as much volume of air as possible from a relative due point (exothermic reaction), the fuel already in cylinder must be burnt completely to extract the most energy (allowing for the boundary layer), a complete burn of fixed fuel = more heat, more heat = more power, basic physics.
Manufacturers go to huge lengths to achieve the perfect/maximum thermal efficiency in engine design striking the perfect balance from a induction temperature and the heating point of the fuel vs permissible exhaust temperature (EGT) whist targeting the idea push/pumping(expansion) cycle or adiabatic process. The problem in tuning a diesel engine for a manufacturer is purely down to controlling EGT relative to particle matter and Nox (nitrogen oxide) emissions the very reason forcing the use of DPF systems.
So how is the damage done? By modifying the lambda (fuel relative to air) the first issue is the over loading of the DPF management cycle as the filter is designed to handle a certain amount of matter vs measured flow vs a oil quality / engine ageing strategy, think of it like this - tuning an engine, it is a given performance air filters, they provide more airflow by using better, more expensive materials.
Currently there is no material solution for DPF to achieve performance increase other than (at best) an increase regeneration cycles to keep flow optimized resulting in increased fuel use for such a regeneration leading to the inevitable shorted life cycle. So adding fuel = Dead DPF.
Turbochargers suffer greatly from tuning ignorance, and are a fundamental component in managing the efficiency of a engine. The compressor map of a turbo dictates the dynamics of the air heating process with the cylinder temperatures vs EGT calibrated precisely known as the 'flame wall' as diesel fuel ignition timing is dictated by the mass vs relative fuel temperature respecting thermodynamic variables / e.g. - the fuel pressure (endothermic reaction), fuel mass (duration), start of injection (timing).
We see issues with calibrations where the mass (duration) is modified, the SOI (timing) is modified along with increased rail pressure resulting in the movement of the flame wall causing a cascade rise in EGT, thus damaging the turbocharger due to the paradox of increased boost pressure only compounding the issue. Another issue born out of over fuelling and flame de-tuning is the sooting of the exhaust wheel of the turbo causing an imbalance of the turbine and jamming of the variable geometry setup where applicable, thus greatly reducing the life of the turbocharger.
Drive line and chassis harmonics - Manufacturers again go to huge length to control engine running frequency and this 'noise' causes long term damage to components. A simple example is the presence of a dual mass flywheel, which is tasked in part to countering this issue in conjunction with tuned engine mounts and phased injection strategies.
-
By not respecting these components in a calibration, all will lead to early failure.
The work is already done in the ECU to increase the performance to a sensible point without compromising the power train. The key is understanding the physics on which the calibration was designed, so the next time you see a youtube video of a vehicle pumping a dyno cell full of black smoke think about what you have read here and the ignorance of some tuners
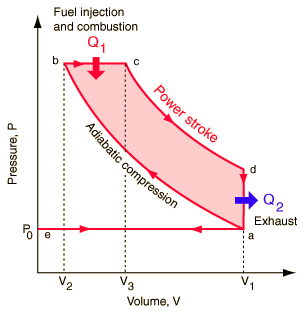